Introduction
United Parcel Service (UPS) is a global logistics company that specializes in package delivery and supply chain management. With over 500,000 employees and a presence in over 220 countries and territories, UPS is one of the largest and most recognizable logistics companies in the world. One of the key components of UPS’s operations is warehouse scan, which is the process of scanning and tracking packages as they move through the company’s warehouses and distribution centers.
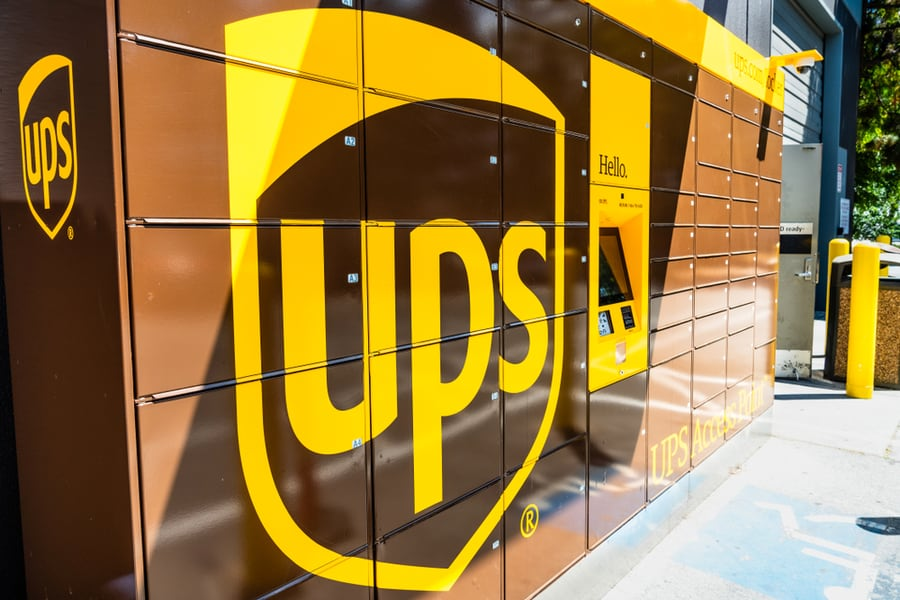
The Importance of Warehouse Scan in UPS Operations
Warehouse scan is a critical component of UPS’s operations, as it allows the company to manage inventory and track packages in real-time. By scanning packages as they move through the warehouse, UPS can ensure that they are properly sorted and routed to their final destination. This helps to minimize errors and delays, which can have a significant impact on customer satisfaction.
In addition to improving accuracy and efficiency, warehouse scan also plays a key role in ensuring timely deliveries. By tracking packages in real-time, UPS can identify potential delays and take corrective action before they become a problem. This helps to ensure that packages are delivered on time, which is critical for businesses and individuals who rely on UPS for their shipping needs.
Overall, warehouse scan is a critical component of UPS’s operations, as it helps to improve accuracy, efficiency, and customer satisfaction.
How Warehouse Scan Works in UPS
The process of warehouse scan in UPS begins when packages are received at the warehouse. Each package is assigned a unique tracking number, which is used to identify and track the package as it moves through the warehouse. The package is then scanned using a handheld scanner or other scanning device, which captures the tracking number and updates the package’s status in the UPS system.
As the package moves through the warehouse, it may be scanned multiple times to track its progress and ensure that it is properly sorted and routed. Once the package is ready for delivery, it is scanned one final time to confirm its destination and ensure that it is loaded onto the correct delivery vehicle.
To support warehouse scan, UPS uses a variety of technologies, including barcode scanning, RFID technology, and automated data capture systems. These technologies help to improve accuracy and efficiency, while also providing real-time visibility into the status of packages as they move through the warehouse.
Benefits of Warehouse Scan for UPS and Its Customers
There are many benefits of warehouse scan for UPS and its customers. One of the primary benefits is improved inventory management and tracking. By scanning packages as they move through the warehouse, UPS can keep track of inventory levels and ensure that packages are properly sorted and routed. This helps to minimize errors and delays, which can have a significant impact on customer satisfaction.
Another benefit of warehouse scan is faster and more accurate deliveries. By tracking packages in real-time, UPS can identify potential delays and take corrective action before they become a problem. This helps to ensure that packages are delivered on time, which is critical for businesses and individuals who rely on UPS for their shipping needs.
Finally, warehouse scan helps to enhance customer satisfaction by providing real-time visibility into the status of packages. Customers can track their packages online or through the UPS mobile app, which allows them to see when their package is expected to arrive and where it is in the delivery process. This helps to reduce anxiety and uncertainty, which can be a major source of frustration for customers.
Common Technologies Used in Warehouse Scan by UPS
UPS uses a variety of technologies to support warehouse scan, including barcode scanning, RFID technology, and automated data capture systems. Barcode scanning is the most common technology used in warehouse scan, as it is simple, reliable, and cost-effective. RFID technology is also used in some cases, particularly for high-value or sensitive packages. Automated data capture systems are used to capture and process data in real-time, which helps to improve accuracy and efficiency.
Challenges Faced in Implementing Warehouse Scan in UPS
Implementing warehouse scan in UPS can be challenging, particularly when it comes to integrating with existing systems and training employees on new technologies. Ensuring data accuracy and security is also a major concern, as any errors or breaches can have a significant impact on customer satisfaction.
To address these challenges, UPS invests heavily in training and development programs for its employees, as well as in technology and infrastructure upgrades. The company also works closely with its customers to ensure that their needs and expectations are met, and that any issues are addressed in a timely and effective manner.
Future of Warehouse Scan in UPS and the Logistics Industry
The future of warehouse scan in UPS and the logistics industry as a whole is bright, with advancements in technology and automation expected to drive increased efficiency and cost savings. As more companies adopt warehouse scan and other advanced logistics technologies, the industry is likely to become more competitive and customer-focused.
One area of particular interest is the use of artificial intelligence and machine learning to improve warehouse scan and other logistics processes. By analyzing large amounts of data in real-time, these technologies can help to identify patterns and trends that can be used to optimize operations and improve customer satisfaction.
Conclusion
In conclusion, warehouse scan is a critical component of UPS’s operations, as it helps to improve accuracy, efficiency, and customer satisfaction. By tracking packages in real-time and using advanced technologies to manage inventory and track shipments, UPS is able to provide fast, reliable, and cost-effective shipping services to businesses and individuals around the world.
As the logistics industry continues to evolve and new technologies emerge, warehouse scan is likely to play an even more important role in enhancing efficiency and customer satisfaction. Businesses that are able to adopt and leverage these technologies are likely to gain a competitive advantage in the marketplace, while also improving their bottom line and enhancing customer loyalty.